Homopolar generator (HPG) pulsed power systems have been workhorse facilities in the pulsed power community. An HPG stores the energy at low power over a longer time interval and then delivers very high power over a short time as shown in Figure 1:
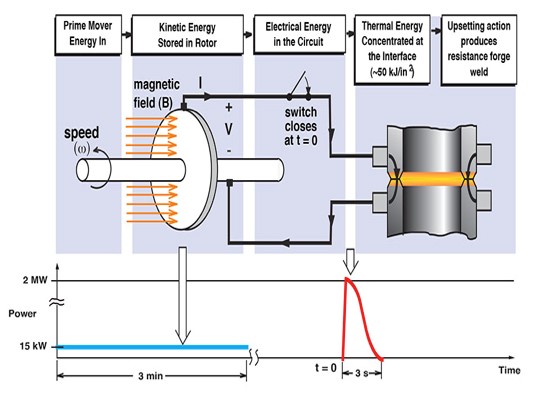
Figure 1: Welding Application: Homopolar operational timeline and power levels
There are both commercial and Federal Government applications for the
technology. In applications where stick welding is altering the chemistry of
the Heat Affected Zone due to long time at temperature, the short welding time
of the HPG process alleviates this problem. As infrastructure upgrades become
increasingly necessary, for instance renovating existing or building new rail
lines, HPG welding can save considerable operational costs for these projects.
With the extensive number of hydraulic fracturing pipelines being installed to
transport shale oil and gas, the HPG process readily transitions to the field
and in-situ welding of these pipelines is feasible. The HPG has also been used
to sinter metal powders. Xray targets in CT scanners are made from sintered
molybdenum and tungsten. The ability to sinter these metals has already been
demonstrated with pulsed compaction. An inexpensive generator could have a
large role to play in this medical field. In the case of transporting nuclear
waste, spent fuel rods must first be welded inside very robust containment. The
HPG could be part of a welding robot that accomplishes this task without
exposing personnel to the radiation. These are just a few of the applications
envisioned for a commercially viable HPG system.
Homopolar pulsed power systems have not transitioned to the commercial market due to machine cost and it is unfortunate that the applications listed here, along with many more yet to be explored, are not advancing. Through support of the US Department of Transportation (USDOT), KAI and CEM engineers were able to explore the design of a low cost HPG system that utilizes technology developments in rotating machinery discovered over the last 30 years that now make the machine commercial viable. Some of the areas explored included ceramic rolling element bearings to replace hydrostatic bearings, commercial electrical brush mechanisms to replace special purpose brushes, variable speed low inertia induction motors to spin the generator as opposed to a high pressure hydraulic motor, complete elimination of high pressure hydraulic auxiliary systems, and use of special purpose bus bars with cross section to react forces.
The current application for the technology steel bridge fabrication has changed little since the 1950s when welding steel began. One of the most time consuming welds to make in bridge fabrication are butt splices between standard mill plates to create plates longer than the steel mill can deliver Figure 2.
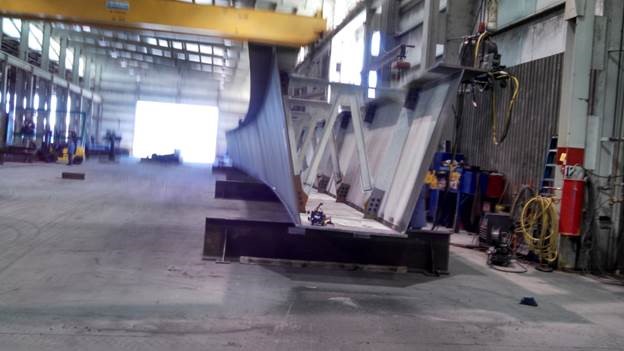
Figure 2. Tub girder in fabrication and the HPG would produce the flange which is the starting point for this structure fabrication
The objective of this program is to conduct a feasibility study to explore and identify innovative welding process variables and/or consumables for application to High Performance Steel, HPS, target cross section 3” x 30”. A subscale HPG, shown in Figure 3, was fabricated to produce weld coupons for to certify the HPG welding process.
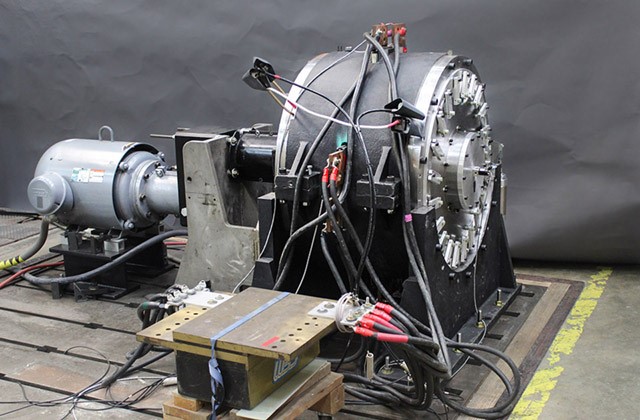
Figure 3: Subscale HPG machine
The HPG welding process is very flexible, as its stored energy is proportional to the moment of inertia of rotor and rotor speed squared, by changing the rotor speed a family of welds is possible.
KAI and its partner UT-CEM just completed the final phase of the USDOT program where a plate welding fixture was mated to the subscale HPG to produce coupons by third party independent metallurgical evaluation Figure 4.
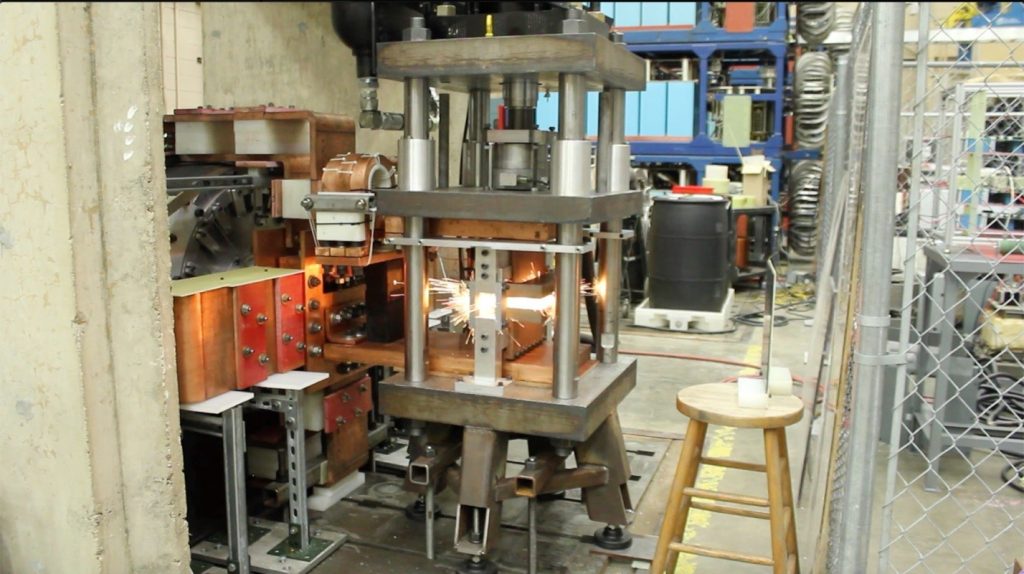
Figure 4. Plate welding fixture interfaced to subscale HPG to produce coupons for weld property evaluation.
The results achieved as a result of identifying the most significant welding process factors, tempering the weld specimen and conducting metallurgical evaluation in compliance with the bridge welding specification, D1.5, are described in the following bullets:
- For the first time, the tensile specimen broke in the base material well away from the weld or heat affected zone.
- The side bend had no flaws and did not show the hard bump in the region of the weld line as seen on earlier bends.
- Residual stresses disappeared in flow patterns in macros and showed uniform grain size.
- There was no retained austenite that would change to martensite over time.
More info about this project can be found at: